Ceramic Powder Compaction Press
2023-07-04 10:29:59
Ceramic powder compaction press is suitable for pressing zirconia, alumina, silicon carbide, aluminum nitride, silicon nitride and other powder products pressing and forming, is a commonly used powder molding machine, with three beams and four columns, four beams and four columns of various structures.
The four-beam four-column hydraulic press we introduce below is specially designed for pressing zirconia ceramic powder. Compared with the three-beam and four-column hydraulic press, there is one more demolding beam, which is mainly used for installing the mold cavity and sliding up and down to demold, which can realize two-way pressurization, floating pressing, automatic demolding, simplify production, and improve production efficiency.
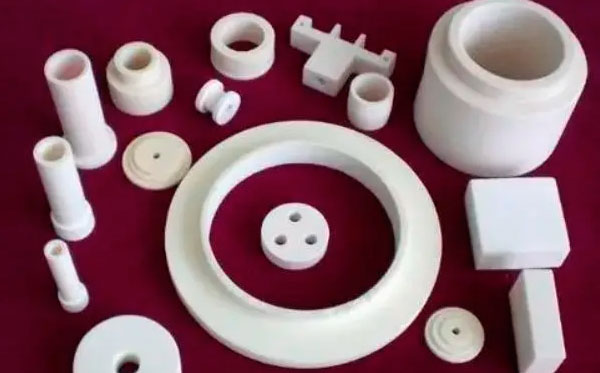
Manufacturing process of ceramic powder compaction press:
1. Design and planning:
According to the needs of users and market needs, design and plan the overall structure and function of the hydraulic press.
Determine the main parameters of the ceramic powder forming hydraulic press, such as working pressure, table size, driving mode, etc.
2. Parts processing:
According to the design drawings, the individual parts of the ceramic powder forming hydraulic press are processed. This includes metal structural parts, hydraulic cylinders, tables, etc. CNC machine tools, lathes, milling machines, grinding machines and other equipment are used for the processing and forming of parts. Heat treatment, surface treatment and other processes on key parts to improve their performance and durability.
3. Component assembly:
The machined parts are assembled. This includes assembling hydraulic cylinders, hydraulic pumps, tubing, electrical components, etc.
Check and adjust the mounting position and interface connections of the individual components to ensure their accuracy and tightness.
4. Hydraulic system installation:
Install hydraulic systems, including hydraulic tanks, hydraulic pumps, pressure valves, control valves, etc.
Carry out the pipeline connection and sealing treatment of the hydraulic system to ensure the normal operation of the hydraulic system.
5. Electrical system installation:
Porcelain powder compaction press installs electrical systems, including electrical control cabinets, electrical components, sensors, control panels, etc.
Carry out wiring and connection of electrical systems, carry out necessary electrical commissioning and testing.
6. Debugging and testing:
Commissioning and testing of assembled hydraulic presses. This includes start-up and operation tests of hydraulic systems, lifting and press-fit tests of workbenches, etc.
Check the functions and performance indicators of ceramic powder forming hydraulic presses to ensure their stable and reliable operation.
7. Quality inspection and adjustment:
Comprehensive quality inspection of ceramic powder forming hydraulic presses, including appearance quality, dimensional accuracy, hydraulic performance and other aspects.
Based on the inspection results, the hydraulic press is adjusted and optimized to ensure that it meets the design requirements and relevant standards.
When operating ceramic powder compaction presses, special attention needs to be paid to the following:
1. Ceramic powder has high hardness and brittleness, easy to produce wear and chipping, please operate carefully to avoid accidents.
2. During operation, according to the characteristics of ceramic powder and the requirements of the forming process, reasonable selection of parameters such as pressure and time.
3. The contact parts such as ceramic powder forming hydraulic press, four-beam and four-column hydraulic press, and mold should be flat and smooth to ensure the surface quality of the molded parts.
The four-beam four-column hydraulic press we introduce below is specially designed for pressing zirconia ceramic powder. Compared with the three-beam and four-column hydraulic press, there is one more demolding beam, which is mainly used for installing the mold cavity and sliding up and down to demold, which can realize two-way pressurization, floating pressing, automatic demolding, simplify production, and improve production efficiency.
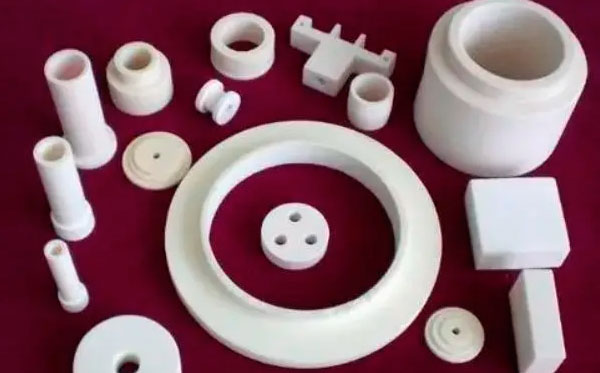
Manufacturing process of ceramic powder compaction press:
1. Design and planning:
According to the needs of users and market needs, design and plan the overall structure and function of the hydraulic press.
Determine the main parameters of the ceramic powder forming hydraulic press, such as working pressure, table size, driving mode, etc.
2. Parts processing:
According to the design drawings, the individual parts of the ceramic powder forming hydraulic press are processed. This includes metal structural parts, hydraulic cylinders, tables, etc. CNC machine tools, lathes, milling machines, grinding machines and other equipment are used for the processing and forming of parts. Heat treatment, surface treatment and other processes on key parts to improve their performance and durability.
3. Component assembly:
The machined parts are assembled. This includes assembling hydraulic cylinders, hydraulic pumps, tubing, electrical components, etc.
Check and adjust the mounting position and interface connections of the individual components to ensure their accuracy and tightness.
4. Hydraulic system installation:
Install hydraulic systems, including hydraulic tanks, hydraulic pumps, pressure valves, control valves, etc.
Carry out the pipeline connection and sealing treatment of the hydraulic system to ensure the normal operation of the hydraulic system.
5. Electrical system installation:
Porcelain powder compaction press installs electrical systems, including electrical control cabinets, electrical components, sensors, control panels, etc.
Carry out wiring and connection of electrical systems, carry out necessary electrical commissioning and testing.
6. Debugging and testing:
Commissioning and testing of assembled hydraulic presses. This includes start-up and operation tests of hydraulic systems, lifting and press-fit tests of workbenches, etc.
Check the functions and performance indicators of ceramic powder forming hydraulic presses to ensure their stable and reliable operation.
7. Quality inspection and adjustment:
Comprehensive quality inspection of ceramic powder forming hydraulic presses, including appearance quality, dimensional accuracy, hydraulic performance and other aspects.
Based on the inspection results, the hydraulic press is adjusted and optimized to ensure that it meets the design requirements and relevant standards.
When operating ceramic powder compaction presses, special attention needs to be paid to the following:
1. Ceramic powder has high hardness and brittleness, easy to produce wear and chipping, please operate carefully to avoid accidents.
2. During operation, according to the characteristics of ceramic powder and the requirements of the forming process, reasonable selection of parameters such as pressure and time.
3. The contact parts such as ceramic powder forming hydraulic press, four-beam and four-column hydraulic press, and mold should be flat and smooth to ensure the surface quality of the molded parts.