Cold Forging Press Forming Solution
2023-10-19 14:25:33
Cold forging press is used for making small components from ductile materials. Impact extrusion process is shown in Fig. Impact extrusion of material is accomplished where the work blank is placed in position over the die opening the punch forces the blank through the die opening causing material to flow plastically around the punch. The outside diameter of the tube is same as diameter of the die, and the thickness is controlled by the clearance between punch and die.
Introduction to Metal Cold Forging Press Forming
Gears, connecting rods, aluminum vacuum cups, jewelry and other items can be seen everywhere in our daily lives and powerful industries, most of which come from the cold extrusion process. The normal temperature metal blank is placed into the mold and processed by high-pressure cold extrusion using a press. The product undergoes embossing, forming, deformation and other processes according to the shape of the mold.
Main Products of Metal Cold Forging Press
Common cold extrusion materials currently include lead, tin, aluminum, copper, zinc and their alloys, low carbon steel, medium carbon steel, tool steel, low alloy steel, stainless steel, gold, platinum, silver and other metals that can be cold extruded forming,
Cold Forging Press Schematic
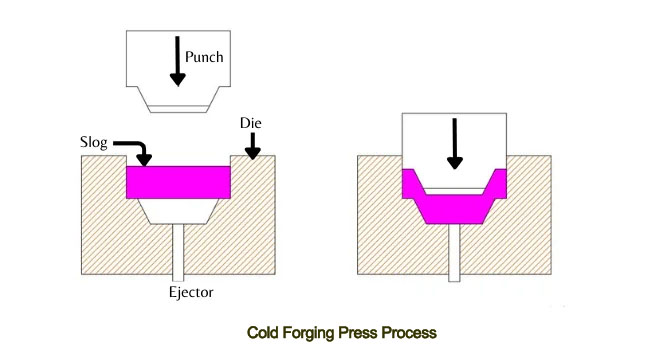
Main Characteristics of Metal Cold Forging Press
It can save a lot of metal materials. Most products can achieve little or no waste through cold forging. In relatively expensive metals (such as gold), cold forging directly replaces turning chip processing.
The processing speed is fast and the efficiency is high. It only takes less than 10 seconds for some products to be cold extruded from the blank to the finished product, which is equivalent to multiple machining centers and lathes. It effectively saves costs for mass production of parts.
The strength of the extruded part of the product extruded by the cold forging press will be improved. The cold forging products are all pressed with high pressure, which slightly improves the strength of the metal. This application is used in the production process of gears, pistons, gear rods and other parts.
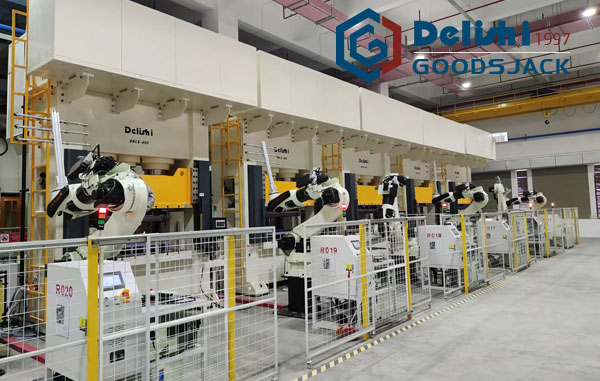
GOODSJACK servo cold forging press has an energy saving effect of 30%-70%, lower noise and failure rate, and is a more environmentally friendly and boss-friendly hydraulic press.
Our company continues to develop and improve cold extrusion technology for the sake of users. Currently, the hydraulic press position control accuracy is as high as ±0.01mm, the pressure control accuracy is as high as ±0.05Mpa, and fully automatic mass production can be achieved. Our cold forging presses have high forming accuracy, strong stability, simple operation, high efficiency and low scrap rate. They are currently widely used at home and abroad.
Introduction to Metal Cold Forging Press Forming
Gears, connecting rods, aluminum vacuum cups, jewelry and other items can be seen everywhere in our daily lives and powerful industries, most of which come from the cold extrusion process. The normal temperature metal blank is placed into the mold and processed by high-pressure cold extrusion using a press. The product undergoes embossing, forming, deformation and other processes according to the shape of the mold.
Main Products of Metal Cold Forging Press
Common cold extrusion materials currently include lead, tin, aluminum, copper, zinc and their alloys, low carbon steel, medium carbon steel, tool steel, low alloy steel, stainless steel, gold, platinum, silver and other metals that can be cold extruded forming,
Cold Forging Press Schematic
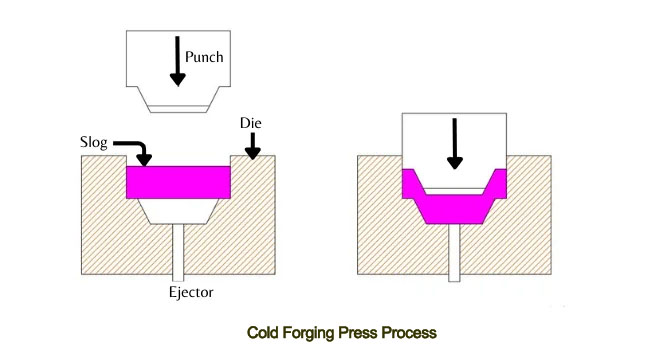
Main Characteristics of Metal Cold Forging Press
It can save a lot of metal materials. Most products can achieve little or no waste through cold forging. In relatively expensive metals (such as gold), cold forging directly replaces turning chip processing.
The processing speed is fast and the efficiency is high. It only takes less than 10 seconds for some products to be cold extruded from the blank to the finished product, which is equivalent to multiple machining centers and lathes. It effectively saves costs for mass production of parts.
The strength of the extruded part of the product extruded by the cold forging press will be improved. The cold forging products are all pressed with high pressure, which slightly improves the strength of the metal. This application is used in the production process of gears, pistons, gear rods and other parts.
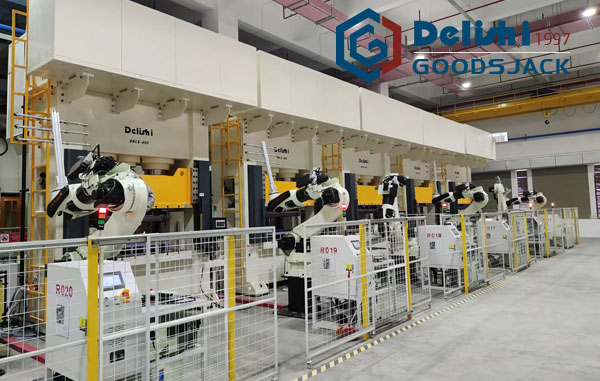
GOODSJACK servo cold forging press has an energy saving effect of 30%-70%, lower noise and failure rate, and is a more environmentally friendly and boss-friendly hydraulic press.
Our company continues to develop and improve cold extrusion technology for the sake of users. Currently, the hydraulic press position control accuracy is as high as ±0.01mm, the pressure control accuracy is as high as ±0.05Mpa, and fully automatic mass production can be achieved. Our cold forging presses have high forming accuracy, strong stability, simple operation, high efficiency and low scrap rate. They are currently widely used at home and abroad.