Hydraulic Presses: How to Prevent Wrinkling in Stamping Parts
2024-05-14 16:50:43
Deep drawn metal staming is a manufacturing process that is used extensively in the forming of sheet metal into cup or box like structures. Pots and pans for cooking, containers, sinks, automobile parts, such as panels and gas tanks, are among a few of the items manufactured by deep drawing metal stamping. Following,Goodsjack/Delishi Hydraulic Machine will introdce how to prevent wrinkling in stamping parts.
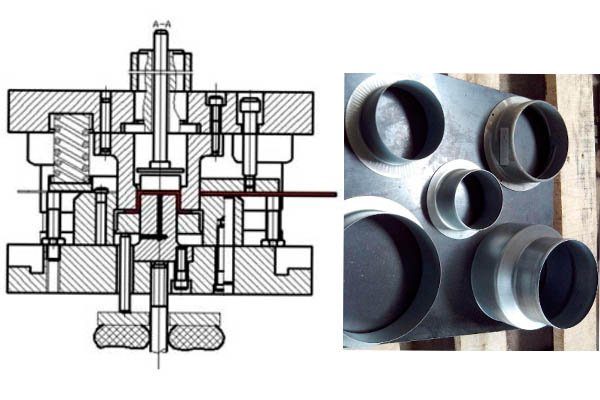
□ The hydraulic press adopts a reasonable pressing device
When a hydraulic press is used, the pressing device tightly presses the deformed part of the blank and exerts pressing force on it to prevent the flange part from arching and causing wrinkles. The size of the pressing force must be appropriate. Pressing devices are divided into two categories: elastic pressing and rigid pressing. Elastic devices are suitable for shallow drawing and rigid devices are suitable for deep drawing.
□ Reasonable use of drawbeads in hydraulic presses
Setting draw beads on the pressing surface of a hydraulic press is an effective and practical method to adjust and control deformation resistance. Draw beads can well regulate the flow of materials, making the flow resistance of each part of the material uniform during the drawing process, so that the amount of material flowing into the cavity is suitable for the needs of the part, and preventing wrinkling in the most cases and cracking in the least cases. The phenomenon. For curved tensile parts with complex shapes, especially those with small flanges, draw beads should be set to increase the radial tensile stress of the stretch to control wrinkling; the draw beads should be set in the radial direction. On the parts with smaller stress, that is, the parts where the sheet material flows easily. For parts with smaller flanges, in order to set draw beads, some material (process supplementary material) can be added appropriately, and this part can be removed during trimming. For drawn parts with large differences in drawing depth, the draw beads should be set in parts with less feed, so that excess material in this part can be prevented from being pulled into the die cavity, thereby preventing wrinkles.
Our engineers suggest that it is best to design the shape of a deep drawing to be as simple as possible. For the primary sheet metal deep drawing process the part will have a flat base and straight sides. If you need deep drawing hydraulic press, please contact us for your hydraulic press solution.
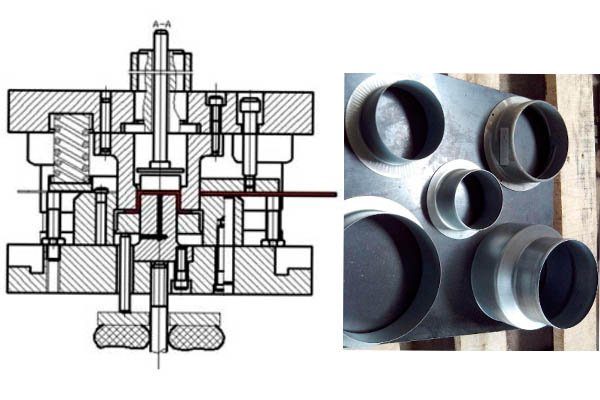
□ The hydraulic press adopts a reasonable pressing device
When a hydraulic press is used, the pressing device tightly presses the deformed part of the blank and exerts pressing force on it to prevent the flange part from arching and causing wrinkles. The size of the pressing force must be appropriate. Pressing devices are divided into two categories: elastic pressing and rigid pressing. Elastic devices are suitable for shallow drawing and rigid devices are suitable for deep drawing.
□ Reasonable use of drawbeads in hydraulic presses
Setting draw beads on the pressing surface of a hydraulic press is an effective and practical method to adjust and control deformation resistance. Draw beads can well regulate the flow of materials, making the flow resistance of each part of the material uniform during the drawing process, so that the amount of material flowing into the cavity is suitable for the needs of the part, and preventing wrinkling in the most cases and cracking in the least cases. The phenomenon. For curved tensile parts with complex shapes, especially those with small flanges, draw beads should be set to increase the radial tensile stress of the stretch to control wrinkling; the draw beads should be set in the radial direction. On the parts with smaller stress, that is, the parts where the sheet material flows easily. For parts with smaller flanges, in order to set draw beads, some material (process supplementary material) can be added appropriately, and this part can be removed during trimming. For drawn parts with large differences in drawing depth, the draw beads should be set in parts with less feed, so that excess material in this part can be prevented from being pulled into the die cavity, thereby preventing wrinkles.
Our engineers suggest that it is best to design the shape of a deep drawing to be as simple as possible. For the primary sheet metal deep drawing process the part will have a flat base and straight sides. If you need deep drawing hydraulic press, please contact us for your hydraulic press solution.