Development Prospects of Servo Hydraulic Presses in The Field of Automotive Parts
2023-12-28 10:41:40
Servo hydraulic presses have been widely used in the field of automotive parts assembly in recent years. The entire assembly process monitoring and evaluation ensures the pass rate of the assembly in one pass. In the field of new energy vehicles, servo presses are more widely used and need to meet more functional requirements.
The main difference between interference assembly in the new energy field and transmission vehicles: Its lightweight requirements produce more precision press-fit assembly parts. Second, the high requirements for motor assembly assembly cannot be met by the capabilities of traditional motor assembly equipment. Third, more electronic control components have been added, and the precision assembly of their connectors requires more precise assembly measurement tools. The servo hydraulic press is an indispensable tool to meet the precision assembly process. Following, we will introduce to you the typical applications of Goodsjack/Delishi servo hydraulic press machine in the field of new energy vehicles.
1. Assembly of lightweight chassis parts
The project requires that aluminum alloy parts need to be assembled with five different shock-absorbing bushings. Through the force and displacement control of the servo press, the different press-fitting position requirements and force requirements for each bushing press-fit are guaranteed, and can be Evaluate based on the different f-s curves of the press-fitting of each bushing to determine whether the press-fitting process of each bushing is qualified.
Assembly of lightweight chassis parts for servo presses
2. Motor lamination assembly
With the rise of domestic new energy vehicles in the past two years, the manufacturing of domestic high-end motors has also been put on the agenda. Kawada helps national brands lay out new energy vehicle motors to form China's "Bosch". The project requires process monitoring of displacement and force during lamination assembly. Through the control of force and displacement of the servo hydraulic press, the press-fitting thickness requirements and output force requirements of the motor laminations are ensured. At the same time, a laser welding machine is integrated into the assembly equipment. The anti-interference design of the servo press integrated system ensures reliable operation of the equipment.
Motor lamination assembly
3.PCB board PIN pin press installation
The project requires that the press-fitting force cannot be too small, otherwise the virtual connection may be poor, and the press-fitting force must not be too large, otherwise the press-fitting deformation may cause a virtual connection. After pressing in, the height of the protrusion at the other end of the PCB board must be within the process requirements. Servo hydraulic presses can be used to press and manufacture battery shells for new energy vehicles. Compared with mechanical presses, deep drawing and other processes can help improve the quality and efficiency of automotive products.

Servo hydraulic press is used for press-fitting of new energy vehicle battery cases
The forming process of the battery case uses multiple dies such as blanking and drawing composite dies, drawing dies, and shaping and trimming dies. Currently, progressive dies are used in conjunction with multi-station presses for production. The progressive die is composed of multiple stations and is a multi-tasking die. In one mold, there can be multiple processes such as punching, blanking, bending, stretching, and trimming. Each station completes different stamping processes in accordance with the process sequence of the product, and cooperates with the feeder to move the material forward according to a fixed step, thus realizing the function of completing multiple stamping processes in one stroke. This production model can reduce the turnover and repeated positioning of multiple sets of molds, improve production efficiency and equipment utilization, facilitate cooperation with automation, and reduce the investment in presses and the transportation and storage of semi-finished products.
The automatic production line of automobile battery shells uses a servo press combined with an NC feeder and a three-dimensional manipulator to realize an automated production mode. Through automatic feeding, automatic output, safety detection, mold identification device, automatic mold changing car and other automation devices, the operation is simple, safe and reliable. In addition, the servo press can be equipped with an optional SIM card remote monitoring system, which has the functions of querying the press monitoring system status, accumulated stamping times, shutdown and working hours, etc., and can keep track of the press production efficiency at any time, which is convenient for enterprise production managers to plan and schedule, and improve Enterprise production efficiency.
Servo press is used for press-fitting of new energy vehicle battery cases
Combined with the current development overview and survey statistics of domestic new energy vehicles, the market demand for battery casings is expected in the future. The future will be the era of the Internet of Things, where products, molds, presses, and peripheral auxiliary equipment will be intelligently integrated through computer networks. The multi-station press is used with a CN feeder and a three-dimensional manipulator. Through automatic mold recognition and automatic detection, and with a remote control module, it can meet the needs of high-level digitalization, networked production, and machine self-organization for this large-volume stamping product. A standardized and unmanned operation mode, thus laying a solid foundation for building a smart factory and realizing smart manufacturing.
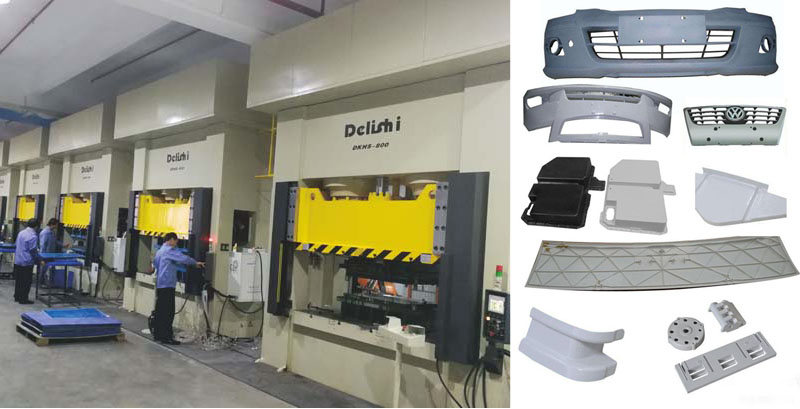
Areas of application for the servo hydraulic press machine:
1. Automotive industry: precision press-fitting of engine components, transmission shaft components, steering gear components, gearbox components, water pump components, brake disc components, oil seals, etc.
2. Motor industry: precision press-fitting of servo motor components, micromotor components (such as spindles, casings, bearings, shafts), etc.
3. Electronics industry: precision pressing and cutting of circuit board components (plug-ins, etc.), electronic parts, communication products, etc.
4. Machinery industry: press-fitting of mechanical parts, automated assembly line applications, life testing of wearing parts, etc.
5. Home appliance industry: pressing and riveting of electrical switches, home appliance accessories, etc.
6. Precision half-cutting of silicone products, etc.
7. Precision pressing of core components of imaging technology
8. Precision pressure testing such as spring performance testing
9. Aviation, scientific research and special equipment applications
10. Other occasions requiring precise pressure and displacement assembly. Such as precision instruments, electronics, bearings, bushings, water pumps, turbochargers, transmissions, gears, etc., automotive shock absorber assembly, precision bearings, bushings, auto parts, water pumps, turbochargers, transmissions Precision press fitting of boxes, gears, automobile chassis parts, rear axles, subframe bushings, etc.
The main difference between interference assembly in the new energy field and transmission vehicles: Its lightweight requirements produce more precision press-fit assembly parts. Second, the high requirements for motor assembly assembly cannot be met by the capabilities of traditional motor assembly equipment. Third, more electronic control components have been added, and the precision assembly of their connectors requires more precise assembly measurement tools. The servo hydraulic press is an indispensable tool to meet the precision assembly process. Following, we will introduce to you the typical applications of Goodsjack/Delishi servo hydraulic press machine in the field of new energy vehicles.
1. Assembly of lightweight chassis parts
The project requires that aluminum alloy parts need to be assembled with five different shock-absorbing bushings. Through the force and displacement control of the servo press, the different press-fitting position requirements and force requirements for each bushing press-fit are guaranteed, and can be Evaluate based on the different f-s curves of the press-fitting of each bushing to determine whether the press-fitting process of each bushing is qualified.
Assembly of lightweight chassis parts for servo presses
2. Motor lamination assembly
With the rise of domestic new energy vehicles in the past two years, the manufacturing of domestic high-end motors has also been put on the agenda. Kawada helps national brands lay out new energy vehicle motors to form China's "Bosch". The project requires process monitoring of displacement and force during lamination assembly. Through the control of force and displacement of the servo hydraulic press, the press-fitting thickness requirements and output force requirements of the motor laminations are ensured. At the same time, a laser welding machine is integrated into the assembly equipment. The anti-interference design of the servo press integrated system ensures reliable operation of the equipment.
Motor lamination assembly
3.PCB board PIN pin press installation
The project requires that the press-fitting force cannot be too small, otherwise the virtual connection may be poor, and the press-fitting force must not be too large, otherwise the press-fitting deformation may cause a virtual connection. After pressing in, the height of the protrusion at the other end of the PCB board must be within the process requirements. Servo hydraulic presses can be used to press and manufacture battery shells for new energy vehicles. Compared with mechanical presses, deep drawing and other processes can help improve the quality and efficiency of automotive products.

Servo hydraulic press is used for press-fitting of new energy vehicle battery cases
The forming process of the battery case uses multiple dies such as blanking and drawing composite dies, drawing dies, and shaping and trimming dies. Currently, progressive dies are used in conjunction with multi-station presses for production. The progressive die is composed of multiple stations and is a multi-tasking die. In one mold, there can be multiple processes such as punching, blanking, bending, stretching, and trimming. Each station completes different stamping processes in accordance with the process sequence of the product, and cooperates with the feeder to move the material forward according to a fixed step, thus realizing the function of completing multiple stamping processes in one stroke. This production model can reduce the turnover and repeated positioning of multiple sets of molds, improve production efficiency and equipment utilization, facilitate cooperation with automation, and reduce the investment in presses and the transportation and storage of semi-finished products.
The automatic production line of automobile battery shells uses a servo press combined with an NC feeder and a three-dimensional manipulator to realize an automated production mode. Through automatic feeding, automatic output, safety detection, mold identification device, automatic mold changing car and other automation devices, the operation is simple, safe and reliable. In addition, the servo press can be equipped with an optional SIM card remote monitoring system, which has the functions of querying the press monitoring system status, accumulated stamping times, shutdown and working hours, etc., and can keep track of the press production efficiency at any time, which is convenient for enterprise production managers to plan and schedule, and improve Enterprise production efficiency.
Servo press is used for press-fitting of new energy vehicle battery cases
Combined with the current development overview and survey statistics of domestic new energy vehicles, the market demand for battery casings is expected in the future. The future will be the era of the Internet of Things, where products, molds, presses, and peripheral auxiliary equipment will be intelligently integrated through computer networks. The multi-station press is used with a CN feeder and a three-dimensional manipulator. Through automatic mold recognition and automatic detection, and with a remote control module, it can meet the needs of high-level digitalization, networked production, and machine self-organization for this large-volume stamping product. A standardized and unmanned operation mode, thus laying a solid foundation for building a smart factory and realizing smart manufacturing.
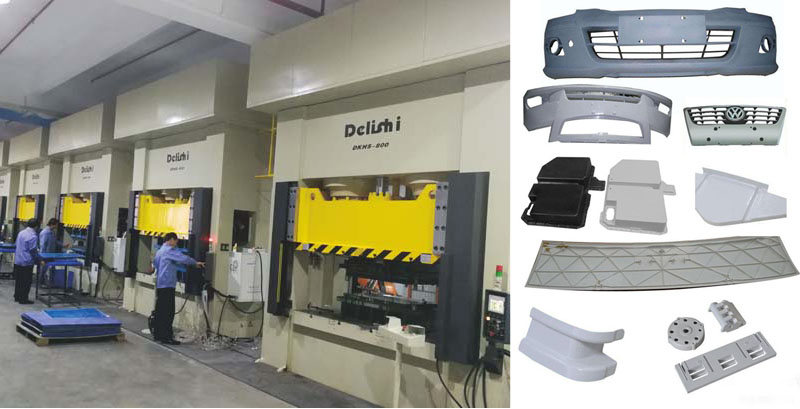
Areas of application for the servo hydraulic press machine:
1. Automotive industry: precision press-fitting of engine components, transmission shaft components, steering gear components, gearbox components, water pump components, brake disc components, oil seals, etc.
2. Motor industry: precision press-fitting of servo motor components, micromotor components (such as spindles, casings, bearings, shafts), etc.
3. Electronics industry: precision pressing and cutting of circuit board components (plug-ins, etc.), electronic parts, communication products, etc.
4. Machinery industry: press-fitting of mechanical parts, automated assembly line applications, life testing of wearing parts, etc.
5. Home appliance industry: pressing and riveting of electrical switches, home appliance accessories, etc.
6. Precision half-cutting of silicone products, etc.
7. Precision pressing of core components of imaging technology
8. Precision pressure testing such as spring performance testing
9. Aviation, scientific research and special equipment applications
10. Other occasions requiring precise pressure and displacement assembly. Such as precision instruments, electronics, bearings, bushings, water pumps, turbochargers, transmissions, gears, etc., automotive shock absorber assembly, precision bearings, bushings, auto parts, water pumps, turbochargers, transmissions Precision press fitting of boxes, gears, automobile chassis parts, rear axles, subframe bushings, etc.