Two Stations Hydraulic Press for Brake Pad Hot FormingUpdate:2024-11-05 Hits:165
The double stations hydraulic press for brake pad hot forming, is a hydraulic press machine specially used for brake pad production. It has two working stations and can form two brake pads at the same time, greatly improving production efficiency. Hydraulic press for brake pad forming is a metal processing technology that mainly uses forging equipment to apply pressure to metal blanks to cause plastic deformation, thereby obtaining brake housing parts with certain shapes, sizes and performances. This process can effectively improve the mechanical properties of the material and make the brake pads more durable.
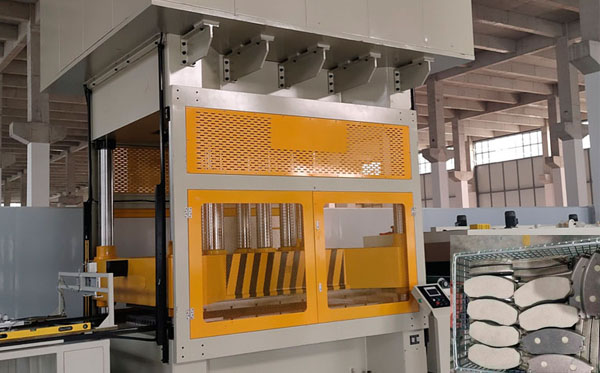
One people can operate 2 hydraulic press for brake pad hot forming, it's save more labor. Following is the featrures of hydraulic press for brake pad hot forming.
High precision: This machine is specially used for making brake pads of motorcycles, cars, trucks, trains, etc. Low energy consumption, low noise, low oil temperature. The main hydro-cylinder adopted no flange structure to improve the leak resistance performance. The high hardness alloy steel used for the main piston rod to increase the wear resistance. The totally enclosed structure for the oil box and electric box is dustproof.
Advanced function: Loading the sheet steel and the powder of the brake pad are done out of the machine to ensure the operation safety. During the pressing, the middle mold will be locked automatically to avoid the leaking of the material. And it has the function of separating automatically. The bottom mold, the middle mold and the top mold can move automatically which will make full use of the mold area, improve the production and save labor.
Brake pad hydraulic press-auto parts automated production line process flow
1. Raw material mixing: Brake pads are basically composed of chemical substances such as steel fiber, graphite, anti-wear agent, resin, etc. The friction coefficient, anti-wear index and noise value are adjusted by the proportional distribution of these raw materials.
2. Hot forming stage: Pour the mixed material into the brake pad forming hydraulic press mold, and then press it from the beginning.
3. Iron sheet processing: After cutting according to different types of iron sheets, harden them by bead impact, and then bond them to the brake pad prototype.
4. Hot pressing stage: Use mechanical soldering iron and brake pads for high-temperature hot pressing to make the two more closely combined. The finished product is called brake pad blank.
5. Heat treatment stage: In order to make the brake pad data more stable and heat-resistant, the brake pad blank needs to be heated for more than 6 hours with this heat treatment machine, and then further processed.
News
- Hydraulic Press Machine for Bicycle Aluminum Alloy Hydroforming2025-06-03
- Hot Stamping Hydraulic Press System2025-04-07
- Happy New Year 20252024-12-31
- Hydraulic Press for Automotive Engine Heat Shield2024-11-28