Hydraulic Hot Forging Press for Golf Club Heads
2024-09-25 10:50:14
The hydraulic hot forging press for golf club heads needs to have enough pressure to plastically deform the metal material and form the shape of the club head. The common pressure ranges from hundreds of tons to thousands of tons. For example, there are hydraulic presses with specifications of 600 tons, 800 tons, 1000 tons, etc. to choose from. The specific pressure requirements will be determined according to factors such as the size of the club head, the complexity of the shape, and the metal material used.
Accuracy Control
○ Stroke control
Accurate stroke control is very important for hot forging of golf club heads. The hydraulic press needs to be able to accurately control the stroke of the slider to ensure that the forming size of the club head meets the design requirements. Generally, the stroke control accuracy is required to be within ±0.1mm, which can ensure the dimensional accuracy and consistency of the club head.
○ Pressure control
During the hot forging process, the hydraulic press needs to maintain a stable pressure output and be able to adjust the pressure according to different forging stages. For example, a higher pressure may be required in the initial forming stage, while a lower pressure may be required in the subsequent finishing stage. The higher the pressure control accuracy, the more guaranteed the quality of the club head. Usually the pressure control accuracy is within ±1%.
○ Speed control
The running speed of the slider also needs to be precisely controlled. Too fast or too slow speed may affect the forming quality of the club head. During the hot forging process, the speed of the slider may need to be adjusted according to different process requirements. For example, different speed settings are required in the stages of fast approach to the workpiece, slow forging, and fast return.
Temperature Control
○ Due to the hot forging process, the metal material needs to be heated to a higher temperature (usually above 1000℃). Therefore, the hydraulic press needs to be equipped with corresponding heating devices, such as heating furnaces or induction heating equipment, to ensure that the metal material can reach the required temperature before forging.
○ At the same time, the hydraulic press also needs to have a good temperature monitoring and control system, which can monitor the temperature of the metal material in real time, and adjust the heating power or forging speed in time according to the temperature change to ensure the stability of the forging process and the quality of the club head.
Die Installation and Replacement System
○ The die is a key component of the hot forging of the golf club head. The hydraulic press needs to be equipped with a convenient and fast die installation and replacement system. The system should be able to ensure the accurate installation and positioning of the mold to ensure the molding accuracy of the club head. At the same time, the mold replacement process should be simple and quick, reduce the downtime of the equipment, and improve production efficiency.
Safety Protection Device
○ The hydraulic hot forging press is a high-power, high-pressure equipment, so the safety protection device is crucial. Common safety protection devices include overload protection, emergency stop button, safety door interlock device, etc. When the equipment has an abnormal situation, these safety protection devices can be activated in time to ensure the safety of the operator.
The production of golf club heads is usually carried out in batches, so the hydraulic press needs to have good stability and reliability and be able to run continuously for a long time without failure. The body structure of the hydraulic press machine should be sturdy and durable, and be able to withstand the high pressure and vibration during hot forging; the hydraulic system should use high-quality hydraulic components to ensure the sealing and stability of the system.
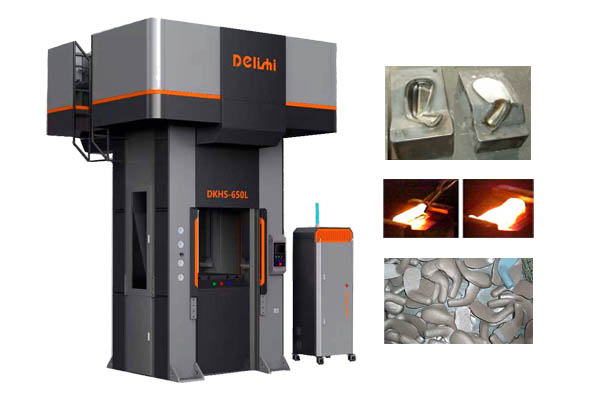
Accuracy Control
○ Stroke control
Accurate stroke control is very important for hot forging of golf club heads. The hydraulic press needs to be able to accurately control the stroke of the slider to ensure that the forming size of the club head meets the design requirements. Generally, the stroke control accuracy is required to be within ±0.1mm, which can ensure the dimensional accuracy and consistency of the club head.
○ Pressure control
During the hot forging process, the hydraulic press needs to maintain a stable pressure output and be able to adjust the pressure according to different forging stages. For example, a higher pressure may be required in the initial forming stage, while a lower pressure may be required in the subsequent finishing stage. The higher the pressure control accuracy, the more guaranteed the quality of the club head. Usually the pressure control accuracy is within ±1%.
○ Speed control
The running speed of the slider also needs to be precisely controlled. Too fast or too slow speed may affect the forming quality of the club head. During the hot forging process, the speed of the slider may need to be adjusted according to different process requirements. For example, different speed settings are required in the stages of fast approach to the workpiece, slow forging, and fast return.
Temperature Control
○ Due to the hot forging process, the metal material needs to be heated to a higher temperature (usually above 1000℃). Therefore, the hydraulic press needs to be equipped with corresponding heating devices, such as heating furnaces or induction heating equipment, to ensure that the metal material can reach the required temperature before forging.
○ At the same time, the hydraulic press also needs to have a good temperature monitoring and control system, which can monitor the temperature of the metal material in real time, and adjust the heating power or forging speed in time according to the temperature change to ensure the stability of the forging process and the quality of the club head.
Die Installation and Replacement System
○ The die is a key component of the hot forging of the golf club head. The hydraulic press needs to be equipped with a convenient and fast die installation and replacement system. The system should be able to ensure the accurate installation and positioning of the mold to ensure the molding accuracy of the club head. At the same time, the mold replacement process should be simple and quick, reduce the downtime of the equipment, and improve production efficiency.
Safety Protection Device
○ The hydraulic hot forging press is a high-power, high-pressure equipment, so the safety protection device is crucial. Common safety protection devices include overload protection, emergency stop button, safety door interlock device, etc. When the equipment has an abnormal situation, these safety protection devices can be activated in time to ensure the safety of the operator.
The production of golf club heads is usually carried out in batches, so the hydraulic press needs to have good stability and reliability and be able to run continuously for a long time without failure. The body structure of the hydraulic press machine should be sturdy and durable, and be able to withstand the high pressure and vibration during hot forging; the hydraulic system should use high-quality hydraulic components to ensure the sealing and stability of the system.