Advantage of Multi-Directional Hydraulic Extrusion PressUpdate:2024-09-06 Hits:148
The multi-directional hydraulic extrusion press mainly generates huge pressure through the hydraulic system. The hydraulic oil is pressed into the hydraulic cylinder under the action of the pump, which pushes the piston motion, which creates a strong squeezing force. This extrusion force can act simultaneously in multiple directions, enabling multi-directional extrusion of the workpiece.
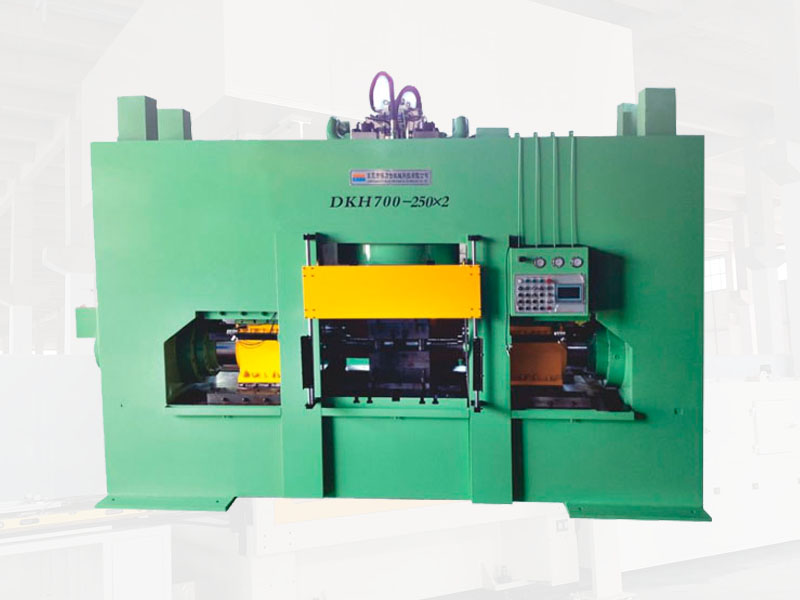
Followings are significant advantages multi-directional hydraulic extrusion presses:
1. Strong squeezing force
It can generate tremendous pressure and can process a wide range of high-hardness and high-strength materials. Whether it is a metallic or non-metallic material, it can achieve precise forming under its strong pressure. This gives it a unique advantage when machining workpieces of some special materials and complex shapes.
2. Multi-directional extrusion capacity
Uniform forming: pressure can be applied from multiple directions at the same time, so that the workpiece is subjected to uniform extrusion force in all directions, so as to ensure that the forming quality of the workpiece is more uniform and stable. For example, when manufacturing metal parts with complex shapes, multi-directional extrusion ensures consistent density and strength across all parts of the part.
Complex shape machining: Complex shape workpieces can be easily processed. By precisely controlling the pressure in different directions, raw materials can be extruded into a variety of complex geometries to meet the needs of different industries for specially-shaped workpieces.
3. High-precision control
Precise pressure control: Equipped with an advanced hydraulic control system, the pressure size and application time can be accurately controlled. This enables the operator to flexibly adjust the pressure parameters according to different processing requirements to ensure the accuracy and stability of the machining process.
Precise stroke control: The stroke of the piston can be accurately controlled, so as to ensure the dimensional accuracy of the workpiece. In some industries that require extremely high dimensional accuracy, such as aerospace and precision machinery manufacturing, the high-precision control ability of multi-directional extrusion hydraulic presses is particularly important.
4. High efficiency and energy saving
Efficient machining: Due to its strong extrusion force and multi-directional extrusion ability, it can complete the processing of workpieces in a short time, which greatly improves the production efficiency. Compared with traditional processing equipment, multi-directional extrusion hydraulic press can reduce processing operations and reduce production costs.
Energy-saving design: The use of advanced hydraulic system and energy-saving technology can effectively reduce energy consumption. During operation, the hydraulic press can automatically adjust the power output according to the actual load situation, avoiding the waste of energy.
5. Strong adaptability
Material adaptability: suitable for extrusion processing of various materials, including metals, plastics, rubber, ceramics, etc. Whether it is a soft material or a hard material, the multi-directional extrusion hydraulic press can be processed reasonably according to its characteristics.
Dimensional adaptability: It can process workpieces of various sizes, from small precision parts to large structural parts. At the same time, by changing the mold and adjusting the parameters, it can quickly adapt to the processing needs of workpieces of different sizes.
6. Safe and reliable
Safety protection device: Equipped with perfect safety protection devices, such as safety grating, emergency stop button, etc., to ensure the personal safety of operators. In the process of processing, once there is an abnormal situation, the equipment can immediately stop running to avoid accidents.
Stable structural design: With a sturdy structural design, it can withstand huge pressure without deformation. At the same time, the hydraulic system has been rigorously tested and optimized to ensure the stability and reliability of the equipment during long-term operation.
What industries are multi-directional extrusion hydraulic presses used in
Multi-directional hydraulic extrusion presses are widely used in the following industries:
1. Aerospace field
Aircraft parts manufacturing: used to manufacture high-strength parts such as aircraft fuselage frames, wing skins, and engine blades. Multi-directional extrusion hydraulic presses ensure that these components have precise dimensions and excellent mechanical properties, meeting the stringent safety and reliability requirements of the aerospace industry.
Spacecraft structural parts processing: In the manufacture of spacecraft, multi-directional extrusion hydraulic presses can be used to process spacecraft shells, fuel tanks and other structural parts. These structural parts need to be characterized by high strength and light weight, and multi-directional extrusion technology can achieve the molding of complex shapes while ensuring the performance of the material.
2. Automobile manufacturing industry
Automobile body parts production: It can be used to produce car body frames, doors, hoods and other components. Multi-directional extrusion can give these components higher strength and better crash safety, while reducing body weight and improving fuel economy.
Auto parts manufacturing: such as the manufacture of key components such as engine blocks, transmission housings, steering knuckles, etc., are also inseparable from multi-directional extrusion hydraulic presses. Multi-directional extrusion enables the machining of complex shapes and improves the accuracy and performance of parts.
3. Metal processing field
Aluminum alloy processing: For the extrusion of aluminum alloy materials, multi-directional extrusion hydraulic press has unique advantages. It can produce all kinds of aluminum alloy profiles, pipes and plates, which are widely used in construction, electronics, transportation and other industries.
Copper alloy processing: In the processing of copper alloys, multi-directional extrusion hydraulic presses can manufacture high-precision copper pipes, copper plates and other products. These products have a wide range of applications in electrical, refrigeration and other fields.
Steel material processing: It can be used for forging and extrusion of steel materials to produce high-strength steel parts, such as gears, shafts, etc.
4. Plastic products field
Engineering plastics processing: For some high-performance engineering plastics, multi-directional extrusion hydraulic press can realize the molding of plastic products with complex shapes. For example, the manufacture of automotive interior parts, electronic and electrical shells, etc.
Plastic pipe production: It can be used to produce all kinds of plastic pipes, such as water supply pipes, drainage pipes, gas pipes, etc. Multi-directional extrusion can ensure that the wall thickness of the pipeline is uniform and the strength is high, which can meet the requirements of different fields.
5. Other industries
Construction industry: used in the production of aluminum alloy doors and windows, curtain wall profiles, etc. for construction. Multi-directional extrusion technology can make these products have better sealing, wind pressure resistance and aesthetics.
Electronics industry: manufacturing electronic equipment shells, radiators and other parts. The multi-directional extrusion hydraulic press can produce high-precision, complex-shaped products to meet the requirements of the electronics industry for miniaturization and lightweight.
Medical device industry: In the manufacture of medical devices, multi-directional hydraulic extrusion presses can be used to produce some high-precision parts, such as surgical instruments, implants, etc. These products need to be dimensionally accurate and biocompatible.