Advantages of Hydraulic Press Forming TechnologyUpdate:2025-03-31 Hits:71
Compared with traditional stamping processes, hydraulic press forming processes have shown significant technical and economic advantages in reducing weight, reducing the number of parts and molds, improving rigidity and strength, and reducing production costs. This process has been increasingly widely used in the industrial field, especially in the automotive industry.
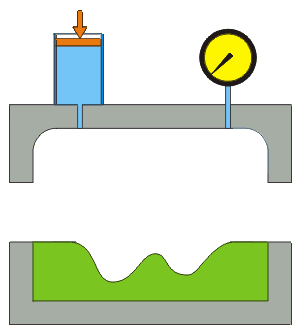
In the automotive industry, aviation, aerospace and other fields, reducing the weight of the structure to save energy during operation is a long-term goal. Hydraulic forming technology is one of the important means to achieve this goal. It uses pipes as blanks, applies ultra-high pressure liquid inside the pipes and assists with axial thrust to make the pipe blank material plastically deformed, so that it fits with the inner wall of the mold cavity to obtain hollow parts that meet technical requirements.
In addition, the hydraulic press forming process also has the ability to integrally form hollow structural parts with changes along the cross section of the component in one go, which is unmatched by traditional stamping and welding processes. Compared with stamping and welding processes, hydraulic forming technology and processes have the following significant advantages.
Reducing weight and saving materials. In the application of typical parts such as automobile engine brackets and radiator brackets, hydroforming technology can achieve a 20% to 40% weight reduction compared to stamping parts; for hollow stepped shaft parts, the weight reduction effect is as high as 40% to 50%.

Reduce the number of parts and molds, and reduce mold costs. Hydroforming usually only requires one set of molds, while stamping parts often require multiple sets. Taking the engine bracket as an example, hydroforming technology reduces the number of its parts from 6 to 1, and the number of radiator bracket parts is also greatly reduced.
Simplify subsequent machining and assembly processes. Hydroforming technology can significantly reduce welding points and processes and improve productivity. For example, the heat dissipation area of the radiator bracket is increased by 43%, the welding points are reduced from 174 to 20, the processes are reduced from 13 to 6, and the productivity is increased by 66%.
Improve strength and stiffness. The hydraulically formed radiator bracket has a 39% increase in stiffness in the vertical direction and a 50% increase in the horizontal direction, which significantly improves its fatigue strength.
Reduce production costs. Statistics show that the production cost of hydraulically formed parts is 15% to 20% lower than that of stamped parts on average, and mold costs are also reduced by 20% to 30%.
Hydraulic press solution & manufacturer - Goodsjack's hydraulic presses can be customized to meet specific requirements, allowing for tailored solutions for complex parts.